Small manufacturing business software is revolutionizing how small-scale manufacturers operate. Efficient inventory management, streamlined production processes, and improved communication are just some of the benefits these software solutions offer. By integrating various aspects of the business, from order processing to customer relationship management (CRM), these systems provide a centralized hub for managing all operations, leading to increased productivity and profitability.
This allows businesses to focus on what truly matters: creating high-quality products and growing their business.
The right software can automate repetitive tasks, reducing manual errors and freeing up valuable time for strategic decision-making. Features such as real-time data tracking, automated reporting, and integrated accounting tools offer unparalleled insight into the business’s performance, enabling informed choices and proactive adjustments to overcome challenges. This level of control and transparency empowers small manufacturers to compete effectively in a dynamic market.
Running a small manufacturing business requires juggling numerous moving parts – from inventory management and production scheduling to quality control and customer relationship management. The right software can be the difference between chaos and controlled efficiency, boosting productivity, reducing errors, and ultimately, increasing profitability. This comprehensive guide explores the essential software solutions available to small manufacturing businesses, helping you navigate the options and choose the tools that best fit your specific needs.
Understanding Your Manufacturing Software Needs: Small Manufacturing Business Software
Before diving into specific software solutions, it’s crucial to assess your business’s unique requirements. Consider the following factors:
- Production Volume: Are you a high-volume manufacturer or a low-volume, custom-order shop? This impacts the complexity of the software you’ll need.
- Product Complexity: Do you manufacture simple or complex products with numerous components and processes? This influences the need for detailed bill of materials (BOM) management and advanced scheduling capabilities.
- Team Size and Structure: How many employees are involved in manufacturing, and what are their roles? The software should support collaboration and efficient workflow management.
- Budget: Software solutions range widely in price. Determine your budget constraints before exploring options.
- Integration Needs: Will the software need to integrate with existing systems like accounting software, CRM, or e-commerce platforms?
Key Software Categories for Small Manufacturers
Several software categories can significantly improve efficiency in a small manufacturing business. Let’s explore some of the most critical:
1. Manufacturing Execution Systems (MES)
MES software provides real-time visibility into your manufacturing process. It tracks production progress, monitors machine performance, manages materials, and collects data for analysis. Key features include:
- Production Scheduling: Optimize production schedules based on demand, capacity, and material availability.
- Real-time Monitoring: Track key performance indicators (KPIs) such as Overall Equipment Effectiveness (OEE) and production cycle times.
- Quality Control: Implement quality checks and track defects to improve product quality and reduce waste.
- Data Collection and Analysis: Gather data on production efficiency, identify bottlenecks, and improve processes.
Example: Many MES solutions are available, ranging from cloud-based options like Katana MRP to more comprehensive enterprise-level systems.
2. Enterprise Resource Planning (ERP) Software
ERP systems integrate various business functions, including manufacturing, finance, human resources, and customer relationship management (CRM). While often associated with larger enterprises, cloud-based ERP solutions are becoming increasingly accessible to small manufacturers. Key benefits include:
- Centralized Data Management: All business data is stored in one system, improving data accuracy and accessibility.
- Improved Collaboration: Different departments can access and share data seamlessly, enhancing communication and collaboration.
- Streamlined Processes: Automate repetitive tasks and improve efficiency across the entire business.
- Better Financial Management: Gain real-time insights into financial performance and improve decision-making.
Example: Software like NetSuite and Odoo offer ERP solutions tailored to small and medium-sized businesses.
3. Computer-Aided Design (CAD) and Computer-Aided Manufacturing (CAM) Software
CAD software is used for designing products, while CAM software translates designs into instructions for manufacturing equipment. These tools are essential for precision manufacturing and efficient production processes. Key features include:
- 3D Modeling: Create detailed 3D models of products.
- Design Optimization: Improve product design for manufacturability and performance.
- Automated Manufacturing: Generate CNC (Computer Numerical Control) programs for automated machine tools.
- Simulation and Analysis: Simulate manufacturing processes to identify potential problems before production.
Example: Fusion 360 from Autodesk is a popular cloud-based CAD/CAM solution for small businesses.
4. Inventory Management Software
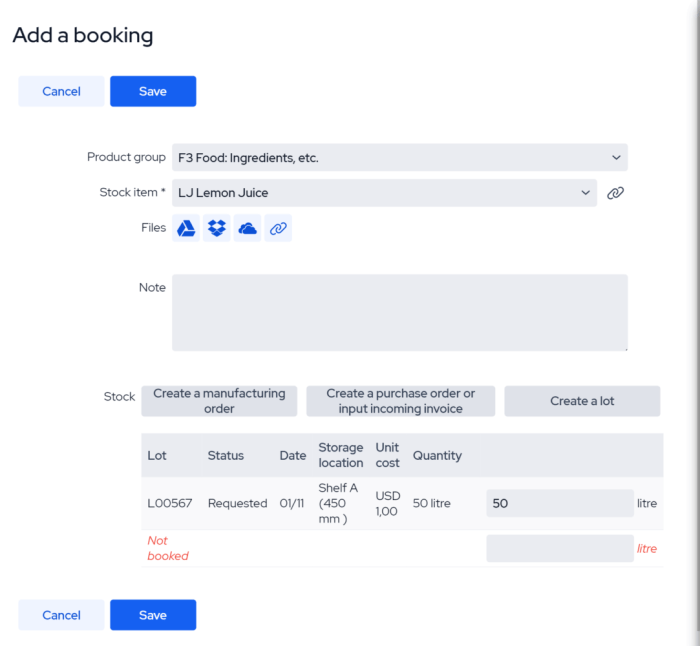
Source: mrpeasy.com
Efficient inventory management is crucial for avoiding stockouts and minimizing storage costs. Software solutions can automate inventory tracking, order management, and forecasting. Key features include:
- Real-time Inventory Tracking: Monitor inventory levels in real-time and receive alerts when stock is low.
- Automated Ordering: Automatically generate purchase orders based on predetermined thresholds.
- Demand Forecasting: Predict future demand to optimize inventory levels.
- Lot and Serial Number Tracking: Track individual items for better quality control and traceability.
Example: Zoho Inventory and Fishbowl Inventory are popular choices for small manufacturers.
5. Customer Relationship Management (CRM) Software
Even in manufacturing, strong customer relationships are essential. CRM software helps manage customer interactions, track sales, and improve customer satisfaction. Key features include:
- Lead Management: Track leads, manage sales opportunities, and convert leads into customers.
- Customer Communication: Communicate with customers efficiently through email, phone, and other channels.
- Sales Tracking: Monitor sales performance and identify areas for improvement.
- Customer Support: Provide efficient customer support and resolve issues promptly.
Example: Salesforce and HubSpot offer robust CRM solutions scalable for businesses of all sizes.
Choosing the Right Software for Your Small Manufacturing Business
Selecting the right software involves careful consideration of your specific needs and budget. Start by identifying your key challenges and the areas where software can provide the most significant impact. Consider a phased approach, starting with essential software and gradually adding more sophisticated tools as your business grows. Don’t hesitate to seek advice from other manufacturers or software consultants.
Frequently Asked Questions (FAQ)
- Q: What is the cost of manufacturing software? A: Costs vary widely depending on the software type, features, and vendor. Some offer subscription-based models, while others require one-time purchases. Expect to invest from a few hundred dollars per month to several thousand, depending on your needs and scale.
- Q: How long does it take to implement manufacturing software? A: Implementation time depends on the software’s complexity and your business’s size and processes. It can range from a few weeks to several months. Proper planning and training are crucial for a smooth transition.
- Q: What are the benefits of using manufacturing software? A: Benefits include improved efficiency, reduced errors, better inventory management, enhanced collaboration, increased productivity, improved quality control, and better decision-making based on data-driven insights.
- Q: Can I integrate different software solutions? A: Yes, many modern software solutions offer APIs (Application Programming Interfaces) that allow for integration with other systems. This is crucial for a seamless workflow.
- Q: What type of training is needed for manufacturing software? A: Most vendors provide training resources, including online tutorials, documentation, and sometimes on-site training. The level of training required depends on the software’s complexity and your team’s technical skills.
Conclusion
Investing in the right software is a critical step in optimizing your small manufacturing business’s efficiency and profitability. By carefully assessing your needs and exploring the various software options available, you can create a streamlined, data-driven operation that positions you for success in a competitive market. Don’t delay – start exploring your options today!
Call to Action
Ready to take your small manufacturing business to the next level? Contact us today for a free consultation to discuss your specific needs and find the perfect software solution for your unique challenges. Let’s build a more efficient and profitable future together!
In conclusion, adopting the right small manufacturing business software is a crucial step for growth and success. The ability to streamline operations, enhance efficiency, and gain valuable insights into business performance provides a significant competitive advantage. By leveraging technology, small manufacturers can overcome operational hurdles, improve customer satisfaction, and ultimately, achieve greater profitability. The investment in such software is not merely an expense, but a strategic move towards a more efficient and prosperous future.
FAQ Compilation
What are the key features to look for in small manufacturing business software?
Key features include inventory management, production scheduling, quality control tracking, CRM integration, and reporting/analytics dashboards. Consider scalability and integration with existing systems.
How much does small manufacturing business software typically cost?

Source: fogwing.io
Pricing varies widely depending on features, scalability, and vendor. Expect to find options ranging from affordable cloud-based solutions to more expensive enterprise-level systems. It’s crucial to compare pricing models (subscription vs. one-time purchase) and factor in implementation costs.
What is the best way to implement new software into an existing business?
A phased approach is generally recommended. Start with a pilot program in a small area of the business to test the software and gather feedback before a full-scale rollout. Adequate training for employees is crucial for successful implementation.
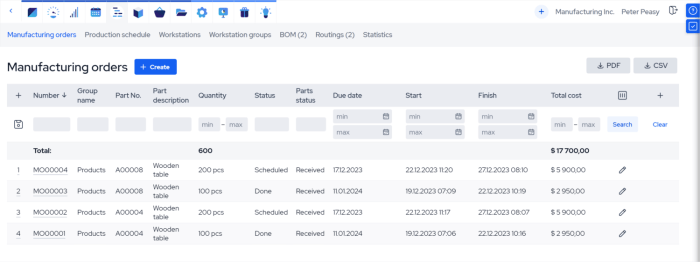
Source: mrpeasy.com
How can I ensure data security with my chosen software?
Look for software providers with robust security measures, including data encryption, access controls, and regular security audits. Read reviews and check for certifications such as ISO 27001.