Manufacturing work order software is revolutionizing how factories and production facilities manage their operations. By centralizing work order creation, tracking, and completion, these systems offer significant improvements in efficiency, accuracy, and overall productivity. This leads to reduced errors, minimized waste, and improved on-time delivery, ultimately boosting profitability and providing valuable data-driven insights for continuous improvement.
These software solutions range from simple, standalone applications suitable for smaller businesses to complex, integrated enterprise resource planning (ERP) systems that handle the entire manufacturing process. Key features often include scheduling, inventory management, resource allocation, quality control tracking, and reporting capabilities. The choice of software depends heavily on the size and complexity of the manufacturing operation, as well as specific needs and budget constraints.
In today’s competitive manufacturing landscape, efficiency and accuracy are paramount. Manufacturing work order software offers a powerful solution to optimize your production processes, reduce errors, and ultimately boost profitability. This comprehensive guide delves into the intricacies of this crucial technology, exploring its features, benefits, and implementation considerations. We’ll cover everything from choosing the right software to maximizing its potential within your manufacturing environment.
Understanding Manufacturing Work Orders and Their Importance
A manufacturing work order is a formal document that authorizes the production of a specific quantity of goods. It details all necessary instructions, including materials required, production steps, deadlines, and quality control checks. Traditionally, these were managed manually, often leading to inefficiencies and errors. Modern manufacturing work order software automates and streamlines this process, significantly improving operational effectiveness.
Key Elements of a Manufacturing Work Order
- Work Order Number: A unique identifier for each order.
- Product Description: Detailed specifications of the item being produced.
- Bill of Materials (BOM): A list of all raw materials and components needed.
- Quantity: The number of units to be manufactured.
- Due Date: The target completion date.
- Work Center/Machine Assignment: Specifies where the work will be performed.
- Labor Requirements: Details the skills and time needed for each stage.
- Quality Control Checks: Artikels inspection points and standards.
Benefits of Implementing Manufacturing Work Order Software
The advantages of adopting manufacturing work order software are substantial and far-reaching. By automating manual processes, businesses can realize significant improvements across various aspects of their operations.
Improved Efficiency and Productivity
- Reduced lead times: Automated scheduling and tracking optimize workflow.
- Minimized downtime: Real-time monitoring prevents production bottlenecks.
- Enhanced resource allocation: Optimized assignment of personnel and equipment.
- Streamlined communication: Real-time updates keep everyone informed.
Enhanced Accuracy and Reduced Errors
- Automated data entry: Minimizes human error in recording and tracking information.
- Real-time inventory tracking: Prevents shortages and delays caused by inaccurate stock levels.
- Improved quality control: Automated checks ensure adherence to standards.
- Reduced waste: Optimized material usage minimizes scrap and rework.
Better Inventory Management
Effective inventory management is critical in manufacturing. Work order software integrates seamlessly with inventory systems, providing real-time visibility into stock levels, enabling accurate forecasting and preventing stockouts or overstocking. This leads to cost savings and improved production planning.
Improved Cost Control and Profitability
By optimizing resource allocation, reducing waste, and improving efficiency, manufacturing work order software directly contributes to lower production costs and higher profitability. Detailed tracking of labor, materials, and overhead expenses allows for better cost analysis and informed decision-making.
Enhanced Collaboration and Communication
The software facilitates seamless communication among different departments and stakeholders, ensuring everyone is on the same page. Real-time updates and dashboards provide transparency and accountability, leading to improved collaboration and project management.
Key Features of Manufacturing Work Order Software
While specific features vary depending on the software provider, some core functionalities are common across most solutions.
Scheduling and Planning
Sophisticated scheduling tools optimize production schedules, considering factors like machine availability, labor resources, and material lead times. This ensures efficient resource utilization and timely order completion.
Material Requirements Planning (MRP)
MRP functionality integrates with inventory management to automatically calculate the required materials for each work order, preventing shortages and minimizing waste. This ensures that the right materials are available at the right time.
Real-time Tracking and Monitoring
Real-time dashboards and reports provide complete visibility into the production process, allowing managers to monitor progress, identify bottlenecks, and take corrective action promptly.
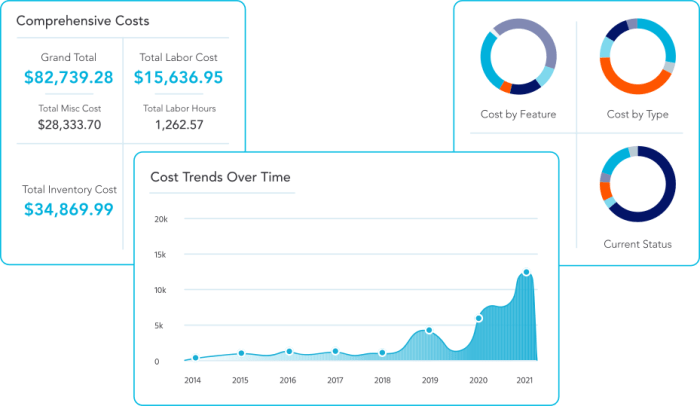
Source: clickup.com
Quality Control and Inspection, Manufacturing work order software
Many solutions include features for managing quality control checks, ensuring that products meet specified standards. This minimizes defects and rework, improving overall product quality.
Reporting and Analytics
Comprehensive reporting capabilities provide valuable insights into production efficiency, cost analysis, and overall performance. This data can be used to identify areas for improvement and optimize processes.
Integration with Other Systems
Seamless integration with Enterprise Resource Planning (ERP) systems, Customer Relationship Management (CRM) systems, and other business applications enhances data flow and operational efficiency.
Choosing the Right Manufacturing Work Order Software
Selecting the right software requires careful consideration of your specific needs and business requirements. Factors to consider include:
- Scalability: Choose software that can adapt to your growing business needs.
- Integration capabilities: Ensure compatibility with existing systems.
- User-friendliness: Select intuitive software that is easy for your team to learn and use.
- Cost: Consider both the initial investment and ongoing maintenance costs.
- Vendor support: Choose a reputable vendor with excellent customer support.
Implementing Manufacturing Work Order Software: A Step-by-Step Guide
- Needs Assessment: Identify your specific requirements and challenges.
- Software Selection: Research and evaluate different software options.
- Data Migration: Transfer existing data to the new system.
- Training: Provide comprehensive training to your team.
- Go-Live: Launch the software and monitor its performance.
- Ongoing Optimization: Continuously refine processes and improve efficiency.
Frequently Asked Questions (FAQ)
- Q: What is the cost of manufacturing work order software? A: Costs vary widely depending on the features, scalability, and vendor. Expect a range from affordable cloud-based solutions to more expensive enterprise-level systems.
- Q: How long does it take to implement manufacturing work order software? A: Implementation time depends on the complexity of your operations and the chosen software. It can range from a few weeks to several months.
- Q: What are the key metrics to track after implementing the software? A: Key metrics include lead times, production efficiency, inventory turnover, defect rates, and overall cost savings.
- Q: Can manufacturing work order software integrate with my existing ERP system? A: Many solutions offer seamless integration with popular ERP systems. Check with the vendor to ensure compatibility.
- Q: What type of training is needed for my employees? A: Comprehensive training is crucial for successful implementation. The vendor should provide training materials and support.
Conclusion: Manufacturing Work Order Software
Implementing manufacturing work order software is a strategic investment that can significantly enhance efficiency, accuracy, and profitability in your manufacturing operations. By carefully considering your needs, selecting the right software, and implementing it effectively, you can unlock the full potential of your manufacturing processes and gain a competitive edge in the market.
References
- Software Advice – Manufacturing Software
- Gartner – Manufacturing Execution Systems (MES)
- Oracle – Manufacturing Execution System
Call to Action: Ready to streamline your manufacturing processes and boost your bottom line? Contact us today for a free consultation and learn how our expert team can help you choose and implement the perfect manufacturing work order software for your business!
In conclusion, the implementation of manufacturing work order software represents a significant step towards modernizing and optimizing the manufacturing process. By streamlining workflows, improving data visibility, and enhancing collaboration, these systems empower businesses to increase efficiency, reduce costs, and gain a competitive edge in today’s dynamic market. The ongoing evolution of these technologies promises even greater advancements in the future, further solidifying their role in the success of modern manufacturing enterprises.
FAQ Insights
What are the benefits of using manufacturing work order software?
Improved efficiency, reduced errors, better inventory management, enhanced collaboration, increased productivity, improved on-time delivery, and data-driven insights for continuous improvement.
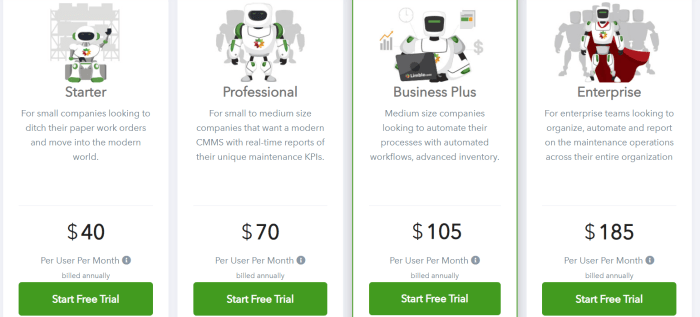
Source: zineddinebk.com
How much does manufacturing work order software cost?
Costs vary significantly depending on the features, scalability, and vendor. Pricing models can include one-time purchases, subscriptions, or a combination of both. It’s crucial to obtain quotes from multiple vendors to compare options.
How do I choose the right manufacturing work order software for my business?
Consider your specific needs, business size, budget, and integration requirements. Research different vendors, compare features, and request demos to find the best fit. Look for software with strong customer support and a proven track record.
Can manufacturing work order software integrate with other systems?
Many systems offer integration capabilities with other business applications, such as ERP systems, CRM systems, and accounting software. This integration enhances data flow and improves overall operational efficiency.